Introduction: Navigating the Global Market for calliper ruler
In the dynamic landscape of precision measurement tools, the calliper ruler stands out as an indispensable instrument for industries ranging from manufacturing and engineering to quality control and research. For international B2B buyers, especially those operating in Africa, South America, the Middle East, and Europe—including emerging markets like Colombia and Argentina—understanding the nuances of sourcing high-quality calliper rulers is crucial to maintaining competitive advantage and ensuring operational excellence.
This guide delves deep into the global market of calliper rulers, offering a comprehensive overview tailored to the needs of discerning buyers. It covers the spectrum of product types—from vernier and dial callipers to digital variants—highlighting their unique applications and precision capabilities. Additionally, the guide explores the materials commonly used, such as stainless steel and hardened alloys, emphasizing their impact on durability and measurement accuracy.
Beyond product specifications, the manufacturing processes and stringent quality control standards that define reliable suppliers are examined, enabling buyers to identify trustworthy partners who meet international standards. Cost considerations and pricing dynamics across different regions are analyzed to help buyers optimize procurement budgets without compromising quality.
Key sections also address market trends and challenges specific to regions like Africa and South America, offering actionable insights to navigate import regulations, logistics, and supplier negotiations effectively. A detailed FAQ segment resolves common queries, further empowering buyers to make well-informed sourcing decisions.
By synthesizing technical knowledge with market intelligence, this guide serves as an authoritative resource for international B2B buyers seeking to procure calliper rulers that meet their precision, reliability, and budgetary requirements in a complex global marketplace.
Understanding calliper ruler Types and Variations
Type Name | Key Distinguishing Features | Primary B2B Applications | Brief Pros & Cons for Buyers |
---|---|---|---|
Vernier Calliper | Manual scale with sliding vernier for precise reading; no power needed | Mechanical engineering, metalworking, quality control | + Durable, no batteries needed – Requires skill to read accurately |
Digital Calliper | Electronic display with digital readout; often with metric/imperial toggle | Manufacturing, automotive, aerospace | + Easy to read, fast measurements – Battery dependent, higher cost |
Dial Calliper | Analog dial indicator for measurement reading; mechanical operation | Toolmaking, woodworking, precision machining | + Clear dial display, reliable – Dial can be fragile, less common |
Inside/Outside Calliper | Specialized jaws for measuring internal and external dimensions | Pipe fitting, automotive parts, construction | + Versatile for varied dimensions – May require multiple callipers for complex tasks |
Depth Calliper | Extended rod for measuring depths and recesses | Engineering, mold making, inspection | + Essential for depth measurements – Limited to specific measurement type |
Vernier Calliper:
Vernier callipers are the traditional manual measuring tools featuring a sliding scale and vernier for fine precision. They are highly valued in industries where power sources are limited or reliability is paramount, such as metal fabrication and quality assurance. Buyers should consider the training required for accurate readings and the robustness of materials, especially stainless steel models that resist corrosion in harsh environments common in Africa and South America.
Digital Calliper:
Digital callipers provide quick, easily readable measurements with electronic displays, making them ideal for fast-paced manufacturing and automotive sectors prevalent in Europe and the Middle East. Their ability to switch between metric and imperial units supports international operations. However, buyers must factor in battery life and the potential need for calibration services, which can impact maintenance costs and operational continuity.
Dial Calliper:
Dial callipers use a mechanical dial for measurement display, offering an intuitive analog interface preferred in precision machining and woodworking. Their mechanical nature reduces dependency on electronics, beneficial in regions with inconsistent power supply. However, their dials can be susceptible to damage, so buyers should assess build quality and warranty support when sourcing for industrial use.
Inside/Outside Calliper:
These callipers feature specialized jaws designed to measure both internal and external dimensions, making them versatile for pipe fitting, automotive parts, and construction projects. For B2B buyers, the adaptability to measure diverse dimensions can reduce tooling inventory. Consideration should be given to the accuracy requirements and whether multiple calliper types are needed for complex applications.
Depth Calliper:
Depth callipers include an extended rod to measure depths of holes, recesses, or slots, essential in engineering and mold-making industries. They complement other calliper types by providing measurements that standard jaws cannot. Buyers should evaluate the precision needed and ensure the calliper’s rod length and durability match their specific industrial requirements.
Related Video: CS 198-126: Lecture 12 – Diffusion Models
Key Industrial Applications of calliper ruler
Industry/Sector | Specific Application of calliper ruler | Value/Benefit for the Business | Key Sourcing Considerations for this Application |
---|---|---|---|
Manufacturing & Engineering | Precision measurement of components and assemblies | Ensures product quality and adherence to tight tolerances | Durability, measurement accuracy, and compliance with standards |
Automotive Industry | Measuring engine parts, brake components, and chassis elements | Reduces defects, improves safety, and streamlines quality control | Robustness, ease of use, and calibration traceability |
Aerospace & Aviation | Inspection of critical aircraft parts and assemblies | Guarantees safety, regulatory compliance, and performance | High precision, certified calibration, and corrosion resistance |
Construction & Architecture | On-site measurement for structural elements and fittings | Enhances build accuracy, reduces rework, and accelerates timelines | Portability, ruggedness, and metric/imperial scale versatility |
Metalworking & Fabrication | Measuring thickness, diameter, and depth of metal parts | Improves fabrication accuracy, reduces waste, and supports quality assurance | Material quality (stainless steel), precision, and wear resistance |
In Manufacturing & Engineering, calliper rulers are indispensable for measuring components with precision, ensuring parts fit perfectly within assemblies. This reduces product defects and enhances overall quality control. For international buyers, especially in emerging markets such as Africa and South America, sourcing callipers that comply with international standards and provide reliable accuracy is crucial to maintain competitiveness.
The Automotive Industry relies heavily on calliper rulers for measuring critical engine parts and brake components. Accurate measurements directly impact vehicle safety and performance. Businesses in regions like the Middle East and Europe benefit from callipers that offer durability and easy calibration, supporting rigorous quality assurance processes and minimizing costly recalls or failures.
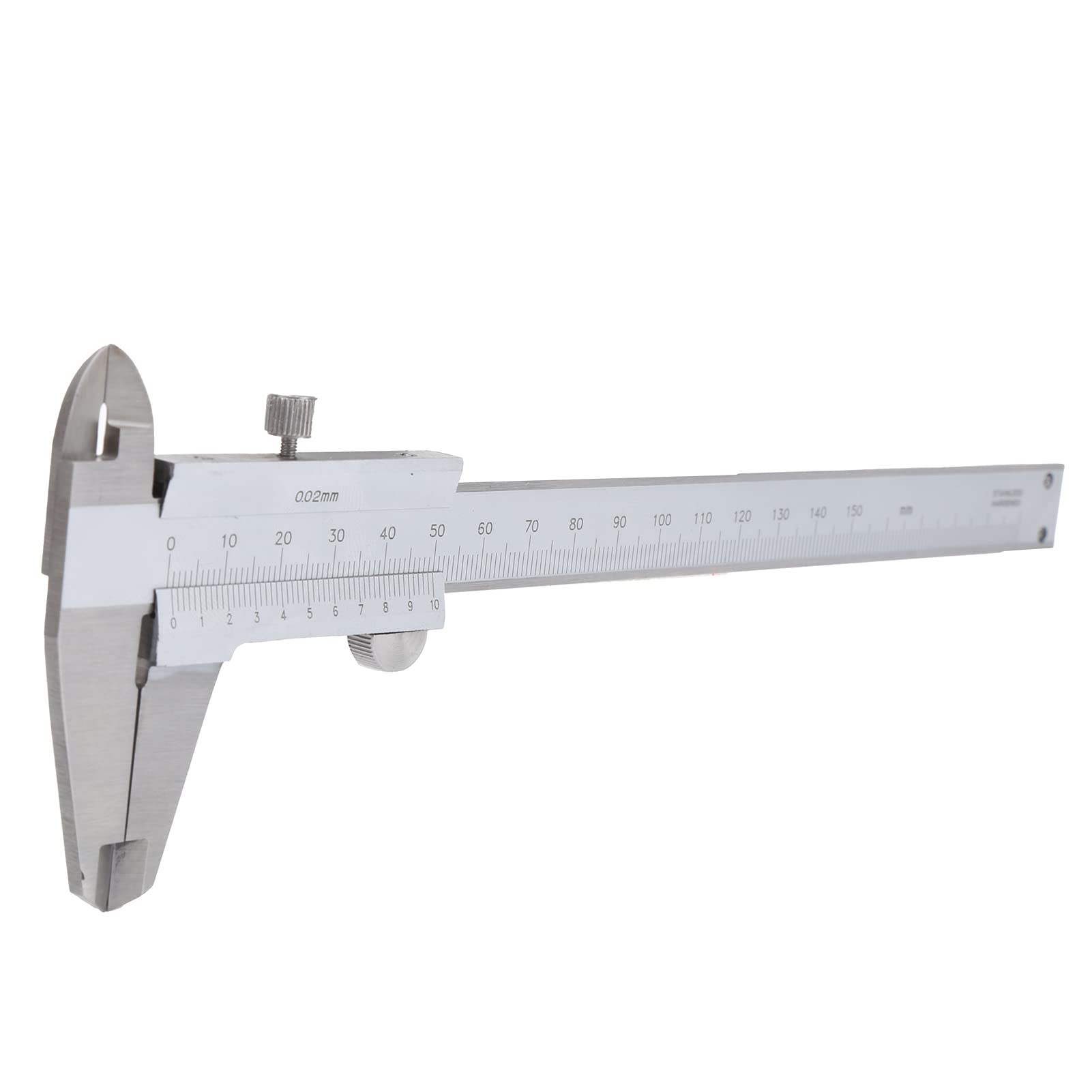
Illustrative Image (Source: Google Search)
In Aerospace & Aviation, calliper rulers are used to inspect aircraft parts where precision is non-negotiable. The tools must meet stringent regulatory requirements and withstand harsh environments. Buyers from Europe and South America should prioritize callipers with certified calibration and corrosion-resistant materials to ensure compliance and longevity in demanding aerospace applications.
For Construction & Architecture, calliper rulers facilitate accurate on-site measurements of structural elements, reducing errors and project delays. Portability and ruggedness are vital for use in diverse environments across Africa and the Middle East. Additionally, the availability of both metric and imperial scales supports international project standards and client requirements.
In Metalworking & Fabrication, calliper rulers measure the thickness, diameter, and depth of metal parts to ensure fabrication accuracy and reduce material waste. Stainless steel callipers with high wear resistance are preferred for durability. Buyers in South America and Europe should focus on sourcing tools that combine precision with robust material construction to withstand industrial conditions and maintain consistent performance.
Related Video: 10 Nifty Uses for Oscillating Multitool Saws
Strategic Material Selection Guide for calliper ruler
When selecting materials for calliper rulers, international B2B buyers must consider performance characteristics, manufacturing feasibility, and regional compliance standards. This is especially critical for buyers in Africa, South America, the Middle East, and Europe, where environmental conditions, industry norms, and cost sensitivities vary significantly. Below is an in-depth analysis of four common materials used in calliper rulers.
Stainless Steel
Key Properties:
Stainless steel is highly corrosion-resistant, durable, and stable under a wide temperature range. It typically withstands temperatures up to 870°C and resists oxidation and chemical exposure, making it ideal for harsh industrial environments.
Pros & Cons:
Pros include excellent durability, resistance to rust and wear, and a premium feel that supports precision measurement. Cons are higher material and manufacturing costs due to machining complexity and the need for corrosion-resistant grades (e.g., 304 or 316 stainless steel).
Impact on Application:
Stainless steel calliper rulers perform well in wet, humid, or chemically aggressive environments, such as oil & gas, marine, and food processing industries. They maintain dimensional stability, critical for precision tools.
Considerations for International Buyers:
Buyers in regions like the Middle East and South America should verify compliance with ASTM A240 or DIN EN 10088 standards to ensure material quality. In Africa and Europe, preference often leans toward certified stainless steel rulers for traceability and quality assurance. Import tariffs and availability of stainless steel grades may affect cost and lead time.
Carbon Steel
Key Properties:
Carbon steel offers high strength and hardness but is less corrosion-resistant than stainless steel. It typically requires protective coatings to prevent rust and has moderate temperature tolerance.
Pros & Cons:
Carbon steel is cost-effective and easier to machine than stainless steel, which can reduce manufacturing time. However, it is prone to corrosion if not properly treated and may require regular maintenance.
Impact on Application:
Ideal for dry, controlled environments or where cost constraints outweigh corrosion concerns. Often used in workshop or indoor industrial settings where exposure to moisture is minimal.
Considerations for International Buyers:
In regions with high humidity or coastal exposure, such as parts of Africa and South America, carbon steel rulers may require additional surface treatments (e.g., black oxide or powder coating). Compliance with regional standards like JIS G4051 (Japan Industrial Standard) or EN 10025 (Europe) can help ensure material consistency.
Aluminum
Key Properties:
Aluminum is lightweight, corrosion-resistant, and easy to machine. It has moderate strength and good thermal conductivity but lower wear resistance compared to steel.
Pros & Cons:
The main advantage is its light weight, making it suitable for portable calliper rulers. It is also cost-effective and resistant to corrosion without additional coatings. However, aluminum is softer, which can lead to quicker wear and less precision over time.
Impact on Application:
Best suited for applications requiring frequent handling and portability, such as fieldwork or educational settings. Not recommended for heavy industrial use where abrasion resistance is critical.
Considerations for International Buyers:
Buyers in Europe and the Middle East often prefer anodized aluminum for enhanced durability and aesthetic appeal. Aluminum sourced from regions with strong environmental regulations (e.g., EU REACH compliance) ensures sustainable procurement. In South America and Africa, availability and cost of anodized aluminum may vary, so buyers should assess local supplier capabilities.
Plastic (Engineering-grade Polymers)
Key Properties:
High-performance plastics like ABS or polycarbonate offer excellent chemical resistance, electrical insulation, and lightweight properties. They have low thermal expansion but limited mechanical strength compared to metals.
Pros & Cons:
Plastic calliper rulers are inexpensive, corrosion-proof, and suitable for non-industrial applications. However, they lack the rigidity and precision of metal rulers and can deform under mechanical stress or high temperatures.
Impact on Application:
Ideal for educational, office, or light industrial use where chemical exposure is a concern but extreme precision is not critical. They are also useful in environments where electrical insulation is needed.
Considerations for International Buyers:
In markets like Africa and South America, plastic callipers may be preferred for cost-sensitive sectors. Compliance with ISO 9001 and relevant RoHS directives is important to ensure product safety and quality. Buyers should also consider UV resistance if products are used outdoors in sunny climates common in the Middle East and Africa.
Material | Typical Use Case for calliper ruler | Key Advantage | Key Disadvantage/Limitation | Relative Cost (Low/Med/High) |
---|---|---|---|---|
Stainless Steel | Precision industrial measurement in harsh environments | Exceptional corrosion resistance and durability | Higher cost and complex manufacturing | High |
Carbon Steel | General workshop and indoor industrial use | Cost-effective and strong | Prone to corrosion without protective coating | Low |
Aluminum | Portable, lightweight callipers for field or educational use | Lightweight and corrosion-resistant | Softer, less wear-resistant | Medium |
Plastic | Educational, office, and light industrial applications | Low cost and chemical resistance | Limited precision and mechanical strength | Low |
In-depth Look: Manufacturing Processes and Quality Assurance for calliper ruler
Manufacturing Processes for Calliper Rulers
The production of high-precision calliper rulers involves several critical stages, each designed to ensure accuracy, durability, and usability. Understanding these stages helps B2B buyers assess supplier capabilities and product quality, especially in international trade contexts where standards and expectations may vary.
1. Material Preparation
Calliper rulers are typically manufactured from stainless steel or high-grade alloy steel due to their corrosion resistance and dimensional stability. The raw material undergoes strict selection and testing before processing:
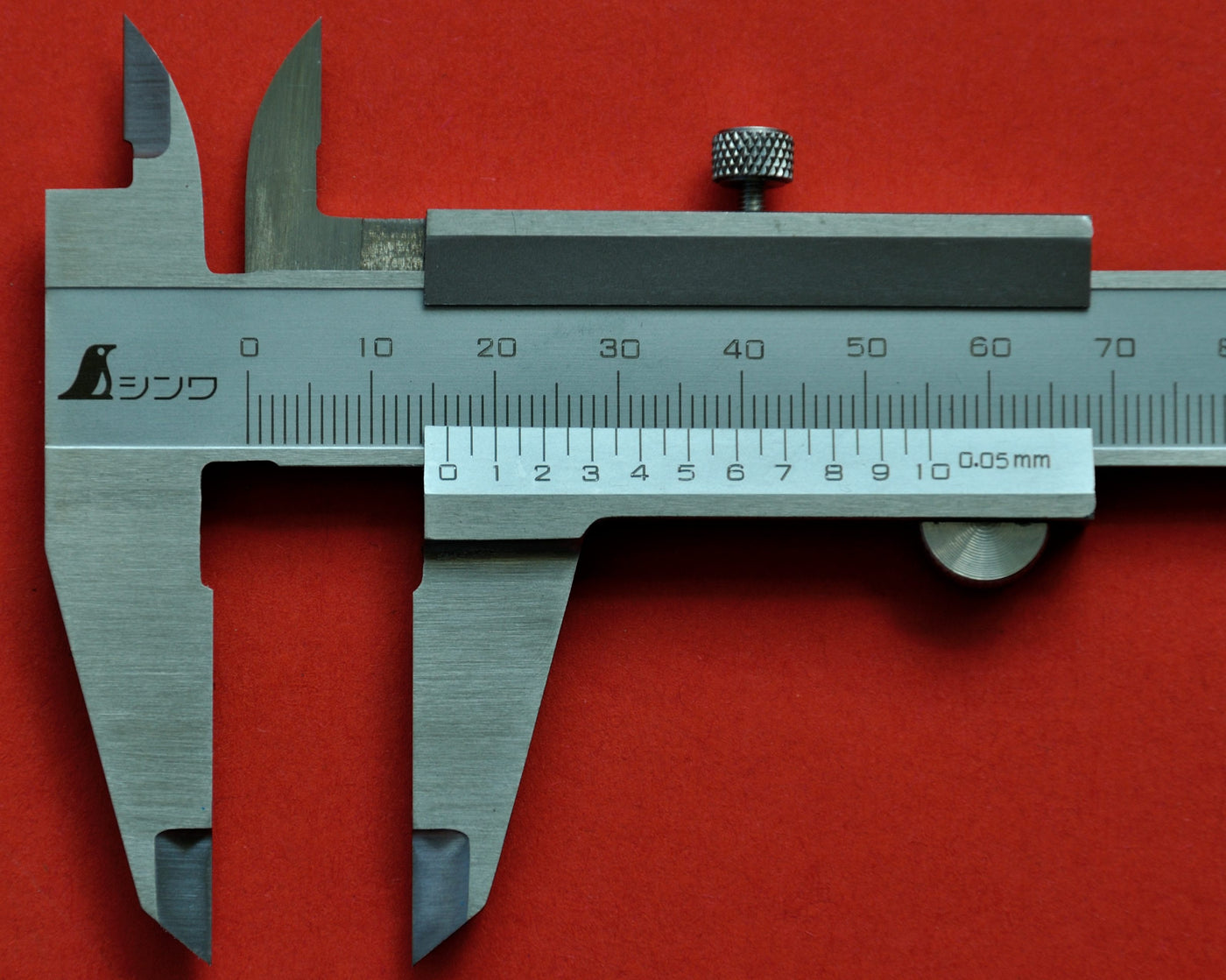
Illustrative Image (Source: Google Search)
- Material Inspection: Verification of chemical composition and mechanical properties via spectrometry and hardness testing.
- Cutting and Blanking: Sheets or rods are cut to size with laser cutting or precision shearing to minimize deformation.
- Surface Preparation: The material surface is cleaned and sometimes pre-treated to enhance adhesion of markings and coatings.
2. Forming and Machining
This phase shapes the calliper ruler components and prepares them for assembly:
- Precision Milling: CNC milling machines carve the scale and jaws with micrometer accuracy.
- Grinding and Polishing: Surfaces are ground to achieve smoothness and flatness, essential for accurate measurement and smooth sliding.
- Marking: Scale graduations are etched using laser engraving or chemical etching, ensuring permanent, high-contrast, and wear-resistant markings.
- Assembly Components: Depending on the model (digital or vernier), assembly may include installing electronic components or mechanical vernier scales.
3. Assembly
Assembly integrates all components into the finished product:
- Component Fitting: Jaws, sliders, and locking screws are precisely fitted to ensure smooth movement without play.
- Calibration: Each unit is calibrated against master gauges to confirm measurement accuracy.
- Lubrication: Sliding parts receive specialized lubricants to enhance performance and longevity.
4. Finishing
The final stage enhances durability and aesthetics:
- Protective Coating: Anti-corrosive coatings or passivation layers may be applied.
- Quality Labels and Certification Marks: Markings indicating compliance with standards (e.g., CE mark) are added.
- Packaging: Products are packaged with care to prevent damage during transit, often including protective cases.
Quality Assurance and Control (QA/QC) in Calliper Ruler Production
Quality control is paramount in manufacturing calliper rulers due to their precision measurement role. International B2B buyers must be familiar with QA/QC practices to ensure they procure reliable, certified products.
Key International and Industry Standards
- ISO 9001: The global benchmark for quality management systems, ensuring consistent production quality and continuous improvement.
- CE Marking: Mandatory for products sold in the European Economic Area (EEA), indicating conformity with health, safety, and environmental protection standards.
- API and Other Industry-Specific Certifications: For specialized applications (e.g., aerospace, oil & gas), compliance with standards from bodies like the American Petroleum Institute (API) may be required.
- National Standards: Buyers from regions such as South America (e.g., IRAM in Argentina) or Africa may require adherence to local metrology and safety standards.
QC Checkpoints Throughout Manufacturing
- Incoming Quality Control (IQC):
– Inspection of raw materials and components for compliance with specifications.
– Verification of material certificates and batch traceability. - In-Process Quality Control (IPQC):
– Continuous monitoring during machining and assembly.
– Dimensional checks using coordinate measuring machines (CMM) and optical comparators.
– Surface finish and marking legibility inspections. - Final Quality Control (FQC):
– Comprehensive functional testing including calibration against standard gauges.
– Verification of smooth operation, locking mechanism reliability, and digital display accuracy (for electronic models).
– Visual inspection for cosmetic defects.
Common Testing Methods
- Dimensional Accuracy Testing: Using master gauge blocks and laser measurement systems to verify scale precision.
- Hardness and Material Integrity Testing: Ensures durability under operational conditions.
- Environmental Testing: Simulates humidity, temperature, and corrosion exposure to assess longevity.
- Repeatability and Resolution Testing: Critical for digital callipers to confirm measurement consistency.
How B2B Buyers Can Verify Supplier Quality Assurance
For international buyers, especially from Africa, South America, the Middle East, and Europe, verifying supplier QC systems is essential to mitigate risk and ensure product compliance.
- Supplier Audits: Conduct on-site factory audits or hire third-party inspection agencies to evaluate manufacturing processes, equipment, and QC protocols.
- Review of Certification Documents: Request and verify copies of ISO 9001 certificates, CE marking declarations, and any industry-specific certifications.
- Quality Control Reports: Obtain sample batch inspection reports detailing IQC, IPQC, and FQC results.
- Third-Party Inspections: Engage independent inspectors to perform random sample testing and verification before shipment.
- Sample Testing: Request product samples for in-house or third-party laboratory testing to validate accuracy and durability claims.
QC and Certification Nuances for International B2B Buyers
- Regional Compliance: Buyers from Colombia, Argentina, Middle Eastern countries, and African markets should ensure that suppliers understand and comply with local import regulations and measurement standards.
- Language and Documentation: QC certificates and reports should be provided in internationally recognized languages (English, Spanish, Arabic, French) to facilitate clear communication.
- Customs and Certification: Some regions may require additional documentation such as customs clearance certificates or national metrology authority approvals.
- After-Sales Support: Verify supplier capabilities for calibration services, warranty, and spare parts availability to maintain tool accuracy over time.
- Digital vs. Mechanical: Digital calliper rulers may have additional software or electronic certifications; buyers should confirm compliance with electromagnetic compatibility (EMC) and safety standards relevant to their markets.
Summary for B2B Buyers
- Prioritize suppliers with robust manufacturing processes that incorporate precision machining, laser etching, and thorough assembly.
- Insist on adherence to ISO 9001 and relevant industry certifications to ensure consistent quality.
- Implement multi-stage QC checks (IQC, IPQC, FQC) and insist on transparent reporting.
- Leverage third-party audits and inspections for objective verification, especially when dealing with new or remote suppliers.
- Understand and comply with regional certification and import requirements to avoid regulatory issues.
- Factor in after-sales calibration and support to maintain product performance and customer satisfaction.
By thoroughly evaluating manufacturing and quality assurance protocols, international B2B buyers can confidently source calliper rulers that meet stringent precision and durability standards, optimizing their supply chain efficiency across diverse markets.
Related Video: Inspection and Quality control in Manufacturing
Comprehensive Cost and Pricing Analysis for calliper ruler Sourcing
Understanding the Cost Components in Calliper Ruler Manufacturing
When sourcing calliper rulers for international B2B procurement, it is crucial to grasp the underlying cost structure that shapes final pricing. The main cost components typically include:
- Materials: The choice of materials—commonly stainless steel, aluminum, or high-grade plastics—directly affects costs. Stainless steel, favored for durability and corrosion resistance, commands a higher price point than plastic but offers better longevity and precision.
- Labor: Skilled labor is essential for precision machining, engraving, and assembly. Labor costs vary by manufacturing location, impacting overall pricing especially when sourcing from regions with different wage levels.
- Manufacturing Overhead: This covers factory utilities, equipment depreciation, and indirect labor, contributing to the baseline production cost.
- Tooling: Precision tools and dies for engraving scales and calibrations represent a significant upfront investment. Custom tooling for unique designs or specifications can increase costs substantially.
- Quality Control (QC): Rigorous inspection, including certification processes for accuracy and compliance with international standards, adds to cost but is critical for ensuring product reliability.
- Logistics: Shipping, customs duties, and import taxes are key cost drivers, particularly for buyers in Africa, South America, the Middle East, and Europe. Freight mode (air vs. sea), packaging, and handling fees should be factored in.
- Margin: Suppliers incorporate profit margins that reflect market demand, competitive positioning, and the value-added services they offer.
Key Pricing Influencers to Consider
Several factors influence the price quotes you will receive from manufacturers or distributors:
- Order Volume and Minimum Order Quantities (MOQ): Larger orders typically attract volume discounts, reducing per-unit costs. However, buyers must balance MOQ with inventory capacity and cash flow.
- Specifications and Customization: Customized calliper rulers with specialized engravings, certifications, or integrated digital displays incur higher prices due to complex tooling and additional QC steps.
- Material Grade and Quality Certifications: Certified stainless steel or precision-grade materials command premium pricing. Certifications such as ISO or calibration certificates add assurance but increase cost.
- Supplier Location and Reputation: Established manufacturers with proven quality records may price higher but offer greater reliability and post-sale support.
- Incoterms and Payment Terms: The agreed Incoterms (e.g., FOB, CIF, DDP) determine which party bears shipping, insurance, and customs costs, influencing the landed cost. Favorable payment terms can also impact pricing negotiations.
Practical Buyer Tips for Cost-Efficient Sourcing
For international buyers, especially in regions like Colombia, Argentina, Nigeria, UAE, and Germany, the following strategies can optimize procurement costs and total cost of ownership:
- Negotiate Beyond Price: Engage suppliers on payment terms, packaging, warranty, and after-sales support to unlock value that offsets raw price differences.
- Assess Total Cost of Ownership (TCO): Consider durability, maintenance, replacement frequency, and calibration needs. A higher upfront price for premium materials and certified accuracy often yields better long-term savings.
- Leverage Consolidated Shipping: Pool orders with other tool purchases or consolidate shipments to reduce per-unit logistics costs, particularly for African and South American buyers facing high freight rates.
- Verify Supplier Certifications and Quality Processes: Avoid cost pitfalls from substandard products by insisting on quality certifications and sample inspections before bulk ordering.
- Understand Local Import Regulations: Anticipate customs duties, taxes, and compliance documentation to avoid unexpected charges or shipment delays.
- Factor in Currency Fluctuations and Payment Risks: Use hedging or secure payment methods to mitigate exchange rate volatility common in emerging markets.
Indicative Pricing Disclaimer
Prices for calliper rulers vary widely depending on specifications, materials, order size, and supplier location. For example, standard stainless steel calliper rulers may range from $5 to $25 per unit at factory gate, excluding shipping and taxes. Customized or certified models can command significantly higher prices. Buyers should obtain multiple quotes and conduct thorough cost analyses tailored to their unique sourcing requirements.
By understanding these cost drivers and pricing influencers, international B2B buyers can make informed decisions, negotiate effectively, and optimize their procurement strategies for calliper rulers across diverse global markets.
Spotlight on Potential calliper ruler Manufacturers and Suppliers
This section looks at several manufacturers active in the ‘calliper ruler’ market. This is a representative sample for illustrative purposes; B2B buyers must conduct extensive due diligence before any transaction. Information is synthesized from public sources and general industry knowledge.
Essential Technical Properties and Trade Terminology for calliper ruler
Key Technical Properties of Calliper Rulers for B2B Buyers
When sourcing calliper rulers for industrial or precision measurement purposes, understanding critical technical properties is essential to ensure product quality, compatibility, and value. Here are the main specifications to consider:
-
Material Grade
High-quality calliper rulers are typically made from stainless steel (often grade 304 or 316), which offers excellent corrosion resistance, durability, and dimensional stability. For buyers in humid or corrosive environments (common in regions like Africa or the Middle East), selecting the right grade ensures longevity and reduces maintenance costs. -
Measurement Scale and Units
Calliper rulers may feature metric (millimeters, centimeters), imperial (inches), or dual-scale markings. For international buyers, especially in South America and Europe, dual-scale tools enhance versatility and reduce errors in cross-standard projects. -
Tolerance and Accuracy
The tolerance level indicates the permissible deviation from the nominal measurement. Typical precision ranges from ±0.02 mm to ±0.05 mm. For manufacturing or engineering applications, tighter tolerances ensure higher measurement reliability, which is critical for quality control. -
Length and Size Options
Calliper rulers come in various lengths, commonly from 6 inches (150 mm) to 24 inches (600 mm) or longer. Selecting the appropriate size depends on the specific measurement tasks and space constraints in the buyer’s operations. -
Finish and Marking Type
The surface finish affects readability and wear resistance. Laser-etched or engraved markings offer superior durability compared to printed scales, which may fade over time. Buyers should prioritize engraving for industrial usage where long-term accuracy is required. -
Certification and Compliance
Certified calliper rulers (e.g., ISO, ASTM standards) come with traceable calibration certificates. This is crucial for buyers who require documented quality assurance for regulatory compliance or internal quality management systems.
Important Trade Terminology for Calliper Ruler Transactions
Understanding common B2B trade terms helps international buyers negotiate better deals, manage expectations, and streamline procurement processes.
-
OEM (Original Equipment Manufacturer)
Refers to products made by a manufacturer who may supply them to other brands for resale. Buyers can request OEM calliper rulers to customize branding or specifications, often at competitive prices. -
MOQ (Minimum Order Quantity)
The smallest number of units a supplier is willing to sell in one order. MOQs vary widely; understanding this helps buyers from smaller markets (e.g., Colombia or Argentina) balance inventory costs and order feasibility. -
RFQ (Request for Quotation)
A formal inquiry sent to suppliers asking for pricing, lead times, and terms. Well-prepared RFQs that clearly specify technical requirements and certifications lead to more accurate and comparable supplier responses. -
Incoterms (International Commercial Terms)
Standardized trade terms defining responsibilities for shipping, insurance, and customs. Examples include FOB (Free On Board) and CIF (Cost, Insurance, Freight). Knowing Incoterms helps buyers from different regions clarify cost allocation and risk during transport. -
Lead Time
The time between placing an order and receiving the product. For international buyers, lead time impacts project schedules and inventory planning. Suppliers with shorter, reliable lead times provide a competitive advantage. -
Calibration Certificate
A document certifying the measurement accuracy of the calliper ruler against recognized standards. Buyers in regulated industries should insist on calibration certificates to ensure compliance and quality assurance.
Practical Insights for International B2B Buyers
- Material and Certification: Prioritize stainless steel calliper rulers with certified calibration to ensure durability and measurement accuracy in diverse climates and industries.
- MOQ and Customization: Engage suppliers offering flexible MOQs and OEM services to tailor products to your market size and branding needs.
- Trade Terms and Logistics: Clearly define Incoterms in contracts to avoid hidden costs and misunderstandings related to shipping and insurance.
- Specification Clarity: Use detailed RFQs to communicate exact technical and quality requirements, enabling precise quotations and minimizing delays.
By focusing on these technical properties and trade terms, buyers from Africa, South America, the Middle East, and Europe can make informed purchasing decisions that optimize cost, quality, and supply chain efficiency.
Navigating Market Dynamics, Sourcing Trends, and Sustainability in the calliper ruler Sector
Market Overview & Key Trends
The global calliper ruler market is experiencing steady growth driven by increasing demand for precision measurement tools across diverse industries such as manufacturing, automotive, aerospace, and construction. For international B2B buyers from regions like Africa, South America (notably Colombia and Argentina), the Middle East, and Europe, understanding the dynamics of this sector is crucial for optimizing procurement and maintaining competitive advantage.
Key market drivers include the rising emphasis on quality control and accuracy in production processes, which fuels the adoption of advanced measuring instruments like digital callipers alongside traditional stainless steel rulers. Technological advancements, such as integration with digital readouts and wireless data transfer, are reshaping the product landscape, enabling faster and more accurate measurements and seamless integration with manufacturing execution systems (MES).
Sourcing trends reveal a growing preference for suppliers offering a broad range of calibrated and certified measuring tools, ensuring compliance with international standards. Buyers from emerging markets are increasingly seeking partnerships with manufacturers who provide customization options, such as metric and imperial scales, as well as specialized callipers for niche applications like pipe thread sizing or aviation mileage measurement.
Market dynamics also reflect a shift toward digitalization and smart tools. European buyers, in particular, prioritize precision and certification, often demanding ISO or NIST-traceable calibration certificates. In contrast, buyers in Africa and South America value cost-effective solutions with robust durability, suitable for harsh operational environments. The Middle East market shows a rising demand for branded, high-quality instruments, especially for oil and gas sector applications.
In summary, B2B buyers must navigate a complex landscape where innovation, certification, and tailored sourcing strategies define success. Engaging with suppliers who combine traditional craftsmanship with modern technology, and who understand regional market requirements, will be key to securing high-value calliper rulers.
Sustainability & Ethical Sourcing in B2B
Sustainability and ethical sourcing are increasingly becoming pivotal considerations in the procurement of calliper rulers. The manufacturing process of precision measuring tools, particularly those made from stainless steel and other metals, has a measurable environmental footprint through raw material extraction, energy consumption, and waste generation.
B2B buyers from Africa, South America, the Middle East, and Europe are progressively demanding transparency in the supply chain, emphasizing responsible sourcing of raw materials and adherence to environmental standards. Suppliers that utilize recycled metals or incorporate eco-friendly production methods, such as energy-efficient manufacturing and waste reduction protocols, stand out as preferred partners.
Green certifications such as ISO 14001 (Environmental Management) and adherence to RoHS (Restriction of Hazardous Substances) standards add significant value to calliper rulers, assuring buyers of reduced environmental impact and compliance with international regulations. Additionally, ethical labor practices and fair trade certifications are critical, particularly for buyers aiming to align their procurement with broader corporate social responsibility (CSR) goals.
Investing in sustainably produced calliper rulers not only supports environmental stewardship but also mitigates risks related to supply chain disruptions due to regulatory changes or reputational damage. For B2B buyers, prioritizing suppliers with clear sustainability commitments and documented impact reduction strategies can lead to long-term cost savings, improved brand image, and alignment with global sustainability initiatives.
Brief Evolution and History
The calliper ruler has evolved significantly from its rudimentary origins as simple measuring sticks to highly sophisticated precision tools. Early versions, dating back to ancient civilizations, were primarily manual instruments used for basic length measurement. The industrial revolution and advancements in metallurgy introduced stainless steel callipers, greatly enhancing durability and measurement accuracy.
The mid-20th century saw the introduction of vernier callipers, which allowed users to measure with finer precision through a sliding scale. More recently, digital callipers have transformed the sector by offering electronic readouts, ease of use, and integration with digital quality control systems, addressing the needs of modern manufacturing.
For B2B buyers, understanding this evolution highlights the importance of selecting calliper rulers that combine historical reliability with modern technological capabilities, ensuring precision, durability, and adaptability to contemporary industrial demands. This historical context also underscores the growing emphasis on certification and standardization in global trade, ensuring interoperability and trust in measurement tools across international markets.
Related Video: Global Trade & Logistics – What is Global Trade?
Frequently Asked Questions (FAQs) for B2B Buyers of calliper ruler
-
How can I effectively vet suppliers of calliper rulers for my international B2B purchase?
To ensure reliability, start by verifying the supplier’s certifications and compliance with international quality standards such as ISO. Request product samples to assess build quality and precision. Check references or reviews from other global clients, especially those in your region (Africa, South America, Middle East, Europe). Confirm the supplier’s manufacturing capabilities and capacity to handle your order size. Additionally, assess their responsiveness and transparency during communication, as this often reflects future collaboration efficiency. -
Is it possible to customize calliper rulers to meet specific measurement or branding requirements?
Yes, many manufacturers offer customization options including scale units (metric, imperial, or dual), material choices (stainless steel, plastic), and branding such as laser engraving or printed logos. For B2B buyers, specifying these requirements upfront during RFQ (Request for Quotation) helps suppliers provide accurate pricing and lead times. Customization is especially valuable for industries requiring certified accuracy or promotional purposes. Always confirm minimum order quantities (MOQs) for customized items, as they may be higher than standard products. -
What are typical minimum order quantities (MOQs) and lead times for calliper ruler orders in international trade?
MOQs vary widely depending on the supplier and product complexity, ranging from as low as 100 units to several thousands for customized callipers. Lead times typically span 3 to 8 weeks, factoring in production, quality assurance, and shipping. Buyers from regions like Africa or South America should also account for additional customs clearance and inland transport time. Negotiating MOQs with suppliers is possible, especially for first-time orders or trial batches, to reduce initial investment risk. -
Which payment terms are most common and secure when sourcing calliper rulers internationally?
Common payment terms include a 30% upfront deposit with the balance paid upon shipment or after inspection. Letters of Credit (LC) are widely used for larger transactions, offering security to both parties. For trusted suppliers, open account terms with net 30-60 days can be negotiated. Always use secure payment platforms and consider escrow services for new suppliers. Clarify all payment terms in the contract to avoid disputes and ensure compliance with your country’s import regulations. -
What quality assurance certifications should I look for when buying calliper rulers for industrial use?
Look for ISO 9001 certification, which ensures the supplier’s quality management system meets international standards. Additionally, calibration certificates traceable to national or international standards (e.g., NIST) are crucial for precision measuring tools. Certified rulers and gauges might come with batch-specific calibration reports. For regulated industries, check for compliance with standards like DIN or ASTM. These certifications guarantee measurement accuracy, critical for quality control in manufacturing and engineering sectors. -
How can I optimize logistics and shipping for international orders of calliper rulers?
Choose suppliers experienced in international shipping with established freight forwarders to ensure smooth customs clearance. Consolidating shipments can reduce freight costs but weigh this against lead times. For buyers in remote regions or countries with complex import regulations, consider suppliers offering DDP (Delivered Duty Paid) terms to minimize logistical risks. Always request detailed shipping documentation, including commercial invoices, packing lists, and certificates of origin, to avoid customs delays. -
What steps should I take if there is a quality dispute with the supplier after receiving the calliper rulers?
First, document the issue thoroughly with photos and measurement discrepancies. Review the purchase agreement and quality standards agreed upon. Engage the supplier promptly with clear evidence and request remediation such as replacement, repair, or refund. If unresolved, involve a third-party inspection or arbitration service specializing in international trade disputes. Maintaining open communication and having a clear contract with dispute resolution clauses helps protect your interests in cross-border transactions. -
Are there regional considerations for sourcing calliper rulers from suppliers in Africa, South America, the Middle East, or Europe?
Yes, regional factors like import tariffs, local standards, and supplier reliability vary significantly. For example, European suppliers often provide high precision and certified tools but may have higher costs and longer lead times. South American and African markets might benefit from regional trade agreements to reduce tariffs. The Middle East offers strategic logistics hubs but requires careful vetting of supplier certifications. Understanding local regulations, currency exchange risks, and regional shipping infrastructure is essential for successful procurement.
Important Disclaimer & Terms of Use
⚠️ Important Disclaimer
The information provided in this guide, including content regarding manufacturers, technical specifications, and market analysis, is for informational and educational purposes only. It does not constitute professional procurement advice, financial advice, or legal advice.
While we have made every effort to ensure the accuracy and timeliness of the information, we are not responsible for any errors, omissions, or outdated information. Market conditions, company details, and technical standards are subject to change.
B2B buyers must conduct their own independent and thorough due diligence before making any purchasing decisions. This includes contacting suppliers directly, verifying certifications, requesting samples, and seeking professional consultation. The risk of relying on any information in this guide is borne solely by the reader.
Strategic Sourcing Conclusion and Outlook for calliper ruler
Strategic sourcing of calliper rulers is critical for businesses aiming to enhance measurement precision and operational efficiency. For international B2B buyers, particularly in regions such as Africa, South America, the Middle East, and Europe, understanding the nuances of supplier capabilities, material quality, and certification standards is essential. Stainless steel models, certified accuracy, and customization options like imprinted branding offer competitive advantages in diverse industrial applications.
Key takeaways for strategic sourcing include:
- Prioritize certified suppliers to ensure measurement reliability and compliance with international standards.
- Evaluate material quality, focusing on durability and corrosion resistance, especially for harsh environments common in mining, manufacturing, and construction sectors.
- Leverage customization to differentiate your offerings and meet specific client or market requirements.
- Consider supply chain resilience by partnering with manufacturers capable of consistent delivery and responsive customer support.
Looking ahead, the demand for precision measuring tools like calliper rulers will continue to grow alongside industrial modernization and quality control advancements. B2B buyers from emerging and established markets should proactively engage with global suppliers to secure innovative, high-quality products that drive productivity and competitive edge. Initiate strategic partnerships today to capitalize on evolving technologies and market trends, ensuring your sourcing strategy remains agile and future-proof.
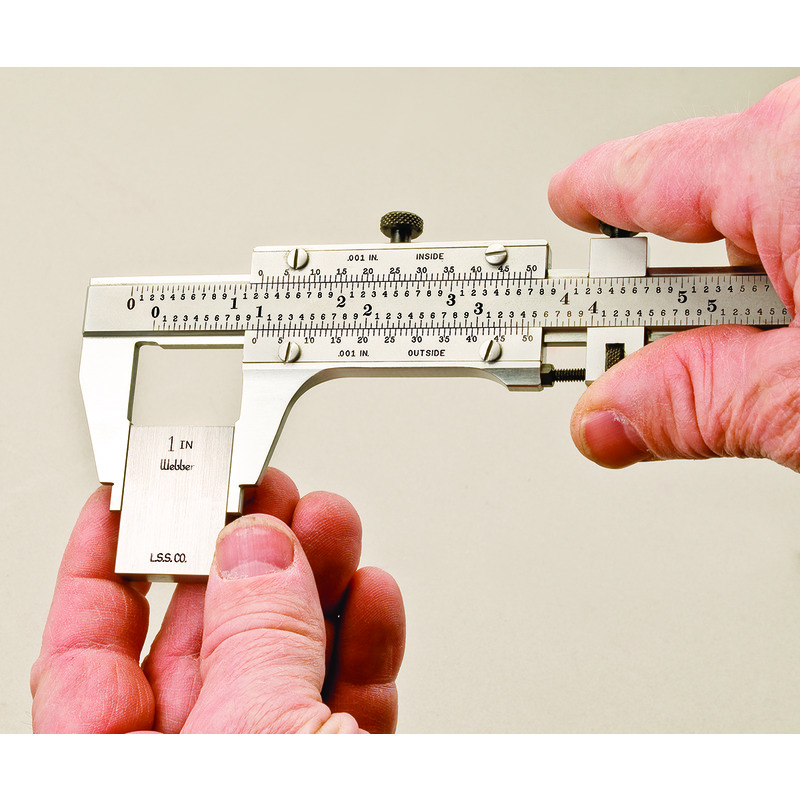
Illustrative Image (Source: Google Search)