Introduction: Navigating the Global Market for cnc wood cutting
The global woodworking landscape is rapidly transforming, driven by the precision, efficiency, and versatility offered by CNC wood cutting technologies. For B2B buyers across Africa, South America, the Middle East, and Europe, selecting the right CNC equipment is no longer a luxury but a strategic imperative. From large-scale furniture manufacturing in São Paulo to bespoke architectural millwork in Dubai or modular interior fit-outs in Berlin, CNC wood cutting machines empower businesses to meet rising demands for customization, accelerated production cycles, and consistent quality standards.
Yet, sourcing CNC wood cutting solutions in an international context involves navigating a complex ecosystem of machine types, material compatibilities, manufacturing quality benchmarks, and supplier reliability. Regional nuances—such as power infrastructure in African manufacturing hubs, regulatory compliance in Europe, or after-sales service challenges in South America—add layers of complexity that require expert insight and careful planning.
This comprehensive guide delivers actionable intelligence tailored for international B2B buyers, covering:
- Detailed overviews of CNC wood cutting machine types and their optimal applications
- Material selection strategies aligned with regional wood species and project requirements
- Critical manufacturing quality and quality control considerations to ensure durability and performance
- Best practices for vetting and partnering with global suppliers, including service and logistics factors
- Transparent cost analysis incorporating acquisition, operation, and regional market dynamics
- In-depth exploration of opportunities and challenges specific to Africa, South America, the Middle East, and Europe
- A robust FAQ section addressing common procurement hurdles and expert solutions
By harnessing these insights, buyers can reduce procurement risks, maximize return on investment, and establish resilient supply chains that support sustainable growth in a competitive global market.
Understanding cnc wood cutting Types and Variations
Type Name | Key Distinguishing Features | Primary B2B Applications | Brief Pros & Cons for Buyers |
---|---|---|---|
CNC Router for Wood | High-speed spindle, flatbed table, 3–5 axis options | Furniture manufacturing, cabinetry, signage | Versatile and fast; moderate 3D capability; requires local support infrastructure |
CNC Wood Lathe | Rotating workpiece, automated shaping tools | Stair parts, balusters, columns | Excellent for cylindrical parts; limited to round shapes only |
5-Axis CNC Wood Machine | Multi-axis simultaneous movement, complex 3D shaping | Custom furniture, mold making, intricate carvings | Enables complex designs; higher cost and training requirements |
CNC Laser Cutter/Engraver | Non-contact laser cutting and engraving | Detailed signage, inlays, prototypes | Highly precise and clean cuts; limited thickness and material types |
CNC Multi-Process Center | Integrates routing, boring, drilling with multi-tool changers | Complex joinery, mass customized furniture | Streamlines production; higher investment and maintenance cost |
CNC Routers for wood are the most widely adopted machines in global woodworking industries due to their adaptability and efficiency. They feature a flatbed table and a high-speed spindle capable of handling various cutting, drilling, and carving tasks. Ideal for large-scale furniture manufacturers and cabinetry producers, these routers support a range of wood types and panel sizes common in markets across Africa, South America, and Europe. Buyers should evaluate the machine’s bed size, spindle power, and compatibility with local software and maintenance capabilities to ensure smooth integration and long-term ROI.
CNC Wood Lathes specialize in shaping cylindrical wooden parts through automated turning. They are indispensable for producing stair balusters, columns, and decorative legs, offering high repeatability and precision. This type is particularly valuable for businesses focused on architectural millwork or artisanal woodworking prevalent in Middle Eastern and South American markets. When sourcing, buyers must consider spindle length, tooling options, and automation features such as multi-tool changers to maximize efficiency for round component production.
5-Axis CNC Wood Machines represent the pinnacle of wood cutting technology, allowing simultaneous movement along five axes for highly intricate 3D shaping without repositioning the workpiece. This capability opens new possibilities for bespoke furniture makers and mold manufacturers seeking to differentiate their offerings. While these machines require a higher upfront investment and advanced operator training, they enable manufacturers in Europe and other innovation-driven regions to meet complex design demands and achieve superior finish quality.
CNC Laser Cutters and Engravers utilize focused laser beams to cut or engrave wood with exceptional precision and minimal material distortion. These machines excel at producing detailed signage, intricate inlays, and rapid prototyping components. Their non-contact nature reduces wear and maintenance, making them attractive for businesses in markets emphasizing high-detail decorative woodwork. However, buyers should note their limitations on cutting thicker or denser wood types, which may restrict application scope in some industrial contexts.
CNC Multi-Process Centers combine routing, boring, and drilling capabilities with automated tool changers, enabling streamlined workflows for complex joinery and customized furniture production. These machines are suited for enterprises aiming to consolidate multiple machining operations into a single platform, boosting throughput and consistency. Although they demand a higher capital investment and maintenance effort, their versatility and efficiency gains are particularly beneficial for large-scale manufacturers in regions with mature woodworking industries, such as Europe and parts of the Middle East.
Related Video: CNC Basics – Make Your First Cut
Key Industrial Applications of cnc wood cutting
Industry/Sector | Specific Application of cnc wood cutting | Value/Benefit for the Business | Key Sourcing Considerations for this Application |
---|---|---|---|
Furniture Manufacturing | Precision cutting and shaping of panels and components | Enhances production speed, repeatability, and product quality | Machine versatility, spindle power, tooling options, local technical support |
Architectural Millwork | Custom moldings, intricate carvings, and decorative trims | Enables complex designs with consistent quality and scalability | Multi-axis capabilities, software compatibility, after-sales training |
Construction & Modular Housing | Cutting structural wood panels for modular assembly | Reduces waste, accelerates build times, improves structural fit | Large bed size, robust frame, regional compliance standards, logistics |
Signage & Branding | Laser cutting/engraving of wooden signs and inlays | Achieves high precision and fine detail for brand differentiation | Laser power, maintenance needs, material thickness limits, supplier proximity |
Artisan & Specialty Woodwork | Production of turned wooden parts like balusters and columns | Automates repetitive shaping, improves accuracy and throughput | Lathe spindle length, tooling change automation, training for complex profiles |
Furniture Manufacturing
In furniture manufacturing, CNC wood cutting machines are extensively used to precisely cut and shape panels, frames, and components for mass production or bespoke orders. This technology solves challenges related to manual inconsistencies and long lead times, enabling manufacturers in regions like South America and Africa to meet growing export demands with consistent quality. Buyers must prioritize routers with adaptable tooling, sufficient spindle power for hardwoods, and reliable after-sales support to ensure minimal downtime in their local markets.
Architectural Millwork
Architectural millwork firms leverage CNC wood cutting to produce custom moldings, ornate trims, and detailed carvings with exacting precision. This is particularly valuable for European and Middle Eastern companies working on luxury interior projects where design complexity and finish quality are paramount. Multi-axis CNC machines that can handle 3D carving and integrate seamlessly with CAD/CAM software are essential. Buyers should evaluate supplier training programs and software compatibility tailored to regional design standards.
Construction & Modular Housing
The construction sector increasingly uses CNC wood cutting to fabricate structural panels and components for modular housing systems, especially in rapidly urbanizing areas of Africa and the Middle East. CNC technology reduces material waste, enhances dimensional accuracy, and speeds up on-site assembly. For buyers, selecting machines with large bed sizes and robust frames capable of handling thick structural panels is critical. Compliance with local building codes and ease of integration with existing workflows are also key considerations.
Signage & Branding
CNC laser cutters and engravers are indispensable for companies specializing in wooden signage, decorative inlays, and branded architectural elements. This application is prominent in European and South American markets where brand differentiation through intricate designs is a competitive advantage. Buyers should focus on laser power specifications, maintenance support, and the ability to process various wood thicknesses. Proximity to suppliers offering quick technical assistance can significantly reduce operational risks.
Artisan & Specialty Woodwork
For artisan workshops and specialty wood manufacturers producing turned components like balusters, columns, and chair legs, CNC wood lathes automate complex shaping processes that traditionally required skilled manual labor. This increases throughput and ensures uniformity, which is particularly beneficial in markets like Brazil and Egypt with strong artisanal traditions. Buyers need to consider lathe spindle length, tooling automation features, and the availability of operator training to maximize machine utility and product quality.
Related Video: Woodworking with 5-axis CNC technology from HOLZ-HER | EPICON CNC machine for wood
Strategic Material Selection Guide for cnc wood cutting
Hardwood
Hardwoods such as oak, maple, and walnut are prized in CNC wood cutting for their density, strength, and attractive grain patterns. These materials exhibit excellent durability and resistance to wear, making them suitable for high-end furniture, cabinetry, and architectural millwork. From a performance standpoint, hardwoods tolerate moderate temperature and pressure during machining without significant deformation, though their density demands robust CNC setups with powerful spindles.
Pros: Hardwoods provide superior aesthetic appeal, longevity, and structural integrity. Their natural resistance to moisture and decay adds value in applications exposed to variable climates.
Cons: They are generally more expensive and harder to machine, requiring slower feed rates and frequent tool maintenance. Production complexity increases, impacting throughput and cost-efficiency.
Application Impact: Hardwoods are ideal for premium products where durability and appearance justify higher costs. They perform well in furniture and decorative elements but may not be cost-effective for large-scale panel production.
International B2B Considerations: Buyers from Europe and the Middle East often prioritize hardwoods for luxury markets, demanding compliance with standards like EN 942 (Furniture) and FSC certification for sustainability. African and South American buyers should consider local hardwood availability and potential import tariffs, balancing cost with quality. Brazil, with its rich hardwood resources, benefits from local sourcing but must ensure CNC machines are calibrated for denser woods. Importers should verify compliance with ASTM D1037 for mechanical properties to ensure consistent quality.
Medium-Density Fiberboard (MDF)
MDF is a widely used engineered wood product composed of wood fibers bonded under heat and pressure. It offers a smooth, uniform surface ideal for CNC routing and finishing. MDF machines easily with standard CNC routers due to its consistent density and absence of grain, enabling precise cuts and intricate designs.
Pros: MDF is cost-effective, readily available worldwide, and easy to machine with minimal tool wear. Its uniformity ensures repeatable results, making it popular for cabinetry, moldings, and signage.
Cons: MDF is susceptible to moisture damage and has lower structural strength compared to solid wood. Dust generated during cutting poses health hazards and requires effective extraction systems.
Application Impact: MDF suits mass production of interior components where surface finish and dimensional accuracy are critical but exposure to moisture is controlled. It is less suitable for outdoor or load-bearing applications.
International B2B Considerations: Buyers in humid regions like parts of Africa and South America should specify moisture-resistant MDF grades (e.g., MR or HMR) compliant with EN 622-5 or ANSI A208.2 standards. European buyers often require E1 or E0 formaldehyde emission ratings for indoor air quality compliance. Middle Eastern markets emphasize dust control and machine filtration capabilities due to stricter workplace safety regulations.
Plywood
Plywood consists of thin wood veneers glued in alternating grain directions, offering excellent strength-to-weight ratio and dimensional stability. It is widely used in furniture, construction, and cabinetry, especially where large panels are needed.
Pros: Plywood resists warping, has good mechanical strength, and machines well on CNC routers. It supports diverse finishes and is available in various grades for structural or decorative use.
Cons: Variability in veneer quality and adhesive types can affect cutting consistency and final product performance. Some plywood types emit higher VOCs, requiring attention to environmental standards.
Application Impact: Plywood is preferred for structural components, cabinetry, and modular furniture where stability and strength are priorities. It is versatile but less suitable for intricate carving compared to MDF or hardwood.
International B2B Considerations: Buyers from Europe and Australia often demand compliance with EN 314 (bonding quality) and CARB Phase 2 for formaldehyde emissions. In South America, sourcing locally produced plywood can reduce costs but requires careful supplier vetting for quality consistency. Middle Eastern buyers should verify fire-retardant grades for compliance with local building codes. African buyers must consider import logistics and potential customs delays impacting lead times.
Bamboo
Bamboo is an increasingly popular sustainable alternative in CNC wood cutting, known for its rapid renewability and unique aesthetic. It offers high tensile strength and natural resistance to moisture and pests, making it suitable for furniture, flooring, and decorative panels.
Pros: Bamboo is lightweight, strong, and eco-friendly, with a distinctive grain pattern that appeals to modern design trends. It machines cleanly with sharp tools and requires less chemical treatment.
Cons: Bamboo’s fibrous structure can cause uneven cutting if tooling is not optimized. It may require specialized CNC programs and tooling to avoid splintering.
Application Impact: Bamboo is ideal for environmentally conscious brands targeting mid-to-high-end markets. Its performance in humid or tropical climates is superior to many woods, broadening application scope.
International B2B Considerations: European and Middle Eastern buyers often seek FSC or PEFC certification for bamboo products, aligning with sustainability mandates. African and South American buyers should evaluate local supply chain maturity and potential for value-added processing to reduce import dependency. Compliance with ISO 22157 (bamboo structural properties) is critical for safety and quality assurance.
Material | Typical Use Case for cnc wood cutting | Key Advantage | Key Disadvantage/Limitation | Relative Cost (Low/Med/High) |
---|---|---|---|---|
Hardwood | Premium furniture, cabinetry, architectural millwork | High durability and aesthetic appeal | Higher machining complexity and cost | High |
Medium-Density Fiberboard (MDF) | Cabinetry, moldings, signage, interior panels | Uniform surface, easy to machine | Vulnerable to moisture, dust hazards | Low |
Plywood | Structural components, cabinetry, modular furniture | Strength and dimensional stability | Variability in veneer quality, VOC emissions | Medium |
Bamboo | Eco-friendly furniture, flooring, decorative panels | Sustainability and moisture resistance | Requires specialized tooling and programming | Medium |
In-depth Look: Manufacturing Processes and Quality Assurance for cnc wood cutting
Manufacturing Processes for CNC Wood Cutting
Successful CNC wood cutting production relies on a well-defined manufacturing workflow that ensures precision, repeatability, and quality. For B2B buyers targeting diverse markets such as Africa, South America, the Middle East, and Europe, understanding the key manufacturing stages and techniques is essential for selecting suppliers that can consistently meet international standards and regional requirements.
1. Material Preparation
The manufacturing process begins with careful selection and preparation of raw wood materials or engineered wood products (e.g., MDF, plywood). Material preparation involves:
- Material grading and inspection: Ensuring wood moisture content, density, and defect levels meet project specifications.
- Cutting to rough sizes: Using band saws or panel saws to produce manageable blanks compatible with CNC machine bed dimensions.
- Surface conditioning: Sanding or planing to create flat, uniform surfaces for accurate CNC processing.
For buyers sourcing from regions with variable raw material quality (such as tropical hardwoods in Africa or South American timber), verifying supplier protocols for moisture control and defect detection is critical to avoid downstream machining issues.
2. CNC Forming and Cutting
This stage involves the core CNC machining operations, where computer-controlled routers, lathes, or multi-axis machines shape the wood components:
- Tool path programming: CAD/CAM software is used to generate precise cutting paths tailored to design files.
- Machining operations: Depending on the machine type, processes include cutting, drilling, carving, engraving, and shaping.
- Tool management: Automated tool changers and spindle speed adjustments optimize cutting efficiency and surface finish.
High-volume manufacturers often implement batch processing with standardized setups to maximize throughput while maintaining dimensional accuracy. Buyers should assess the supplier’s CNC equipment capabilities, software compatibility, and operator expertise, especially when intricate 3D or multi-axis machining is required.
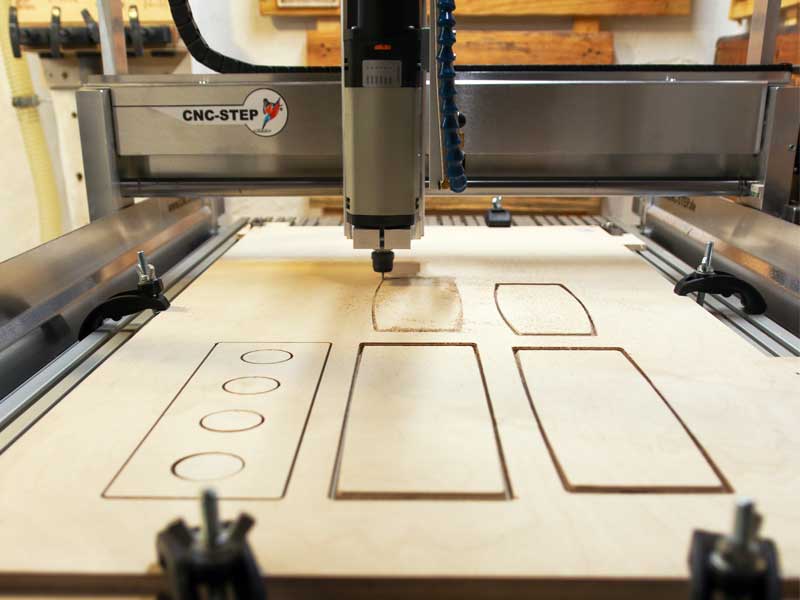
Illustrative Image (Source: Google Search)
3. Assembly and Joining
Post-machining, components may be assembled into sub-assemblies or finished products using:
- Mechanical fastening: Screws, dowels, or brackets for structural integrity.
- Adhesive bonding: Wood glues or laminates for seamless joints.
- Fitting and adjustment: Manual or automated processes to ensure tight tolerances and proper alignment.
In markets where modular furniture or prefabricated wood components dominate (e.g., Middle Eastern construction or European fit-outs), suppliers’ proficiency in assembly quality directly impacts final product performance and ease of installation.
4. Surface Finishing
Finishing processes enhance aesthetics and durability, tailored to end-use and regional preferences:
- Sanding: Automated or manual sanding to achieve smooth surfaces.
- Coating: Application of stains, varnishes, lacquers, or paints, often in controlled environments to ensure uniformity.
- Protective treatments: Anti-fungal or moisture-resistant coatings for wood used in humid climates.
B2B buyers should confirm if finishing processes comply with environmental regulations (e.g., VOC limits in Europe) and align with market expectations for appearance and durability.
Quality Assurance in CNC Wood Cutting
Robust quality assurance (QA) and quality control (QC) frameworks underpin reliable CNC wood cutting production. International buyers must evaluate supplier adherence to global standards and their internal QC rigor to mitigate risks such as dimensional inaccuracies, material defects, or finish inconsistencies.
Relevant International and Industry Standards
- ISO 9001: The globally recognized standard for quality management systems (QMS), emphasizing process control, continuous improvement, and customer satisfaction. Suppliers certified to ISO 9001 demonstrate a systematic approach to quality.
- CE Marking: Mandatory for products sold in the European Economic Area, indicating compliance with health, safety, and environmental protection directives. CNC machinery and finished wood products often require CE certification.
- Industry-Specific Certifications: Depending on application, certifications such as FSC (Forest Stewardship Council) for sustainable sourcing or API standards for wood components in construction may apply.
Buyers from Africa, South America, the Middle East, and Europe should confirm supplier certifications to ensure legal compliance and market acceptance.
Key Quality Control Checkpoints
Quality control is typically segmented into three stages:
- Incoming Quality Control (IQC): Inspection of raw materials for defects, moisture content, and dimensional conformity before entering production.
- In-Process Quality Control (IPQC): Continuous monitoring during machining and assembly to detect deviations early. This includes tool wear checks, dimensional measurements using calipers or coordinate measuring machines (CMM), and visual inspections.
- Final Quality Control (FQC): Comprehensive assessment of finished components or products, verifying surface finish, assembly integrity, and packaging standards.
Suppliers with integrated digital QC systems and traceability protocols provide greater transparency and confidence to international buyers.
Common Testing Methods
- Dimensional Accuracy Tests: Using precision measuring tools and CMMs to ensure parts meet design tolerances.
- Surface Roughness Measurement: Profilometers assess finish quality, critical for paint adhesion or tactile requirements.
- Adhesion and Joint Strength Testing: Mechanical tests validate assembly robustness.
- Moisture Content Analysis: Using moisture meters to prevent warping or cracking in final products.
B2B buyers should request detailed QC reports and evidence of routine calibration of testing equipment.
Verifying Supplier Quality Control Systems
To confidently assess supplier QC capabilities, international buyers should employ a combination of:
- Factory Audits: On-site evaluations focusing on production processes, equipment condition, worker skills, and QC procedures. Audits can be performed by the buyer’s team or independent third-party agencies.
- Review of QC Documentation: Including inspection reports, calibration certificates, non-conformance records, and corrective action logs.
- Third-Party Inspections: Independent inspectors conduct random or batch inspections pre-shipment to verify compliance with specifications.
- Sample Testing: Procuring prototype or pilot batch samples for in-house or laboratory testing to validate quality before mass production.
Leveraging these tools reduces the risk of receiving substandard goods and enables early corrective measures.
QC and Certification Nuances for International B2B Buyers
- Regional Compliance Variations: For example, European buyers prioritize CE marking and strict environmental regulations, while Middle Eastern buyers may emphasize robustness and ease of maintenance due to harsher climates.
- Logistics Impact on QC: Wood products can be sensitive to humidity and handling during transit, making packaging and pre-shipment inspection critical for buyers in tropical or high-humidity regions like parts of Africa and South America.
- Supplier Capability to Adapt: Buyers should verify if suppliers can customize QC protocols to meet local standards or buyer-specific requirements, such as language in documentation or additional testing.
- After-Sales Support and Warranty: Quality assurance extends beyond manufacturing. Buyers should evaluate the supplier’s responsiveness to quality issues post-delivery, including availability of spare parts and technical support.
Actionable Insights for B2B Buyers:
- Demand transparency: Require detailed process descriptions and QC documentation upfront.
- Prioritize certified suppliers: ISO 9001 and CE marks are strong indicators of quality commitment.
- Conduct multi-stage inspections: From IQC to FQC, ensure checkpoints are robust and documented.
- Engage third-party auditors: Especially when sourcing from new or remote regions.
- Adapt QC expectations regionally: Align quality parameters with local market conditions and regulatory frameworks.
- Invest in sample validation: Test product samples thoroughly before committing to bulk orders.
- Ensure supplier flexibility: Ability to customize processes and reporting can be a competitive advantage in global sourcing.
By embedding rigorous manufacturing and quality assurance evaluation into their procurement strategy, international B2B buyers can secure reliable CNC wood cutting partners that drive product excellence and sustainable growth across diverse markets.
Related Video: Amazing scenes。Top 6 Most Popular Factory Manufacturing Videos in China
Comprehensive Cost and Pricing Analysis for cnc wood cutting Sourcing
Key Cost Components in CNC Wood Cutting Sourcing
When evaluating CNC wood cutting solutions, understanding the underlying cost structure is essential for informed decision-making and effective budget allocation. The primary cost components include:
- Materials: The type and quality of wood (hardwood, softwood, engineered boards) and consumables such as tooling inserts and lubricants significantly influence costs. Regional availability of wood species and import duties may further impact material expenses.
- Labor: Skilled labor for machine operation, programming, and maintenance varies by region. Labor costs in Africa and South America tend to be lower compared to Europe or the Middle East, but availability of CNC expertise should be factored in.
- Manufacturing Overhead: This covers utilities (power consumption is a critical factor, especially for high-axis or heavy-duty machines), factory space, and indirect support functions. Energy costs differ widely across regions, affecting operational expenses.
- Tooling: Precision cutting tools and replacement parts are recurring costs. High-quality tooling improves finish and longevity but comes at a premium. Buyers should consider tool compatibility and supplier support for replacements.
- Quality Control (QC): Investments in inspection equipment, certifications (e.g., CE, ISO), and process controls ensure product consistency but add to upfront and ongoing costs.
- Logistics: Freight charges, customs duties, and insurance vary greatly depending on shipment origin and destination. Bulk shipments reduce per-unit freight but increase inventory holding costs.
- Supplier Margin: Pricing includes supplier profit margins, which fluctuate based on brand reputation, machine sophistication, and after-sales service offerings.
Influential Pricing Factors for International Buyers
Several factors shape the final price of CNC wood cutting machines and services, especially relevant for buyers across Africa, South America, the Middle East, and Europe:
- Order Volume and Minimum Order Quantity (MOQ): Larger volume orders typically yield better unit pricing. For manufacturers in emerging markets, consolidating orders or partnering with regional distributors can unlock volume discounts.
- Specifications and Customization: Machines with advanced features such as 5-axis capability, automated tool changers, or laser integration command higher prices. Custom-built solutions tailored to specific wood types or production processes also increase costs.
- Material Quality and Certifications: Compliance with international standards (e.g., CE marking for Europe) and use of premium-grade components elevate costs but reduce risk and improve market acceptance.
- Supplier Factors: Established manufacturers with proven track records and global support networks often price higher but offer better reliability and service. New entrants may offer aggressive pricing but entail higher risk.
- Incoterms and Delivery Terms: The choice between FOB, CIF, DDP, or EXW terms affects who bears shipping, customs clearance, and insurance costs. Buyers should clarify responsibilities to avoid unexpected expenses.
Strategic Buyer Tips for Cost-Efficient Sourcing
To optimize procurement outcomes and total cost of ownership (TCO), international B2B buyers should consider the following best practices:
- Negotiate Beyond Price: Focus on value-added services such as extended warranties, training, spare parts availability, and after-sales support. These can significantly reduce lifecycle costs and downtime.
- Assess Total Cost of Ownership: Look beyond initial machine price to include installation, commissioning, operator training, maintenance, energy consumption, and spare parts logistics—especially important in regions with limited technical infrastructure.
- Leverage Regional Insights: Understand local market dynamics such as power reliability in Africa, import tariffs in South America, or compliance requirements in Europe to anticipate hidden costs.
- Optimize Logistics: Consolidate shipments when possible and select Incoterms that align with your company’s import capabilities. Engage freight forwarders experienced in CNC equipment to reduce delays and damage risks.
- Validate Supplier Credentials: Request references and quality certifications to ensure the supplier meets your region’s regulatory standards and operational expectations.
- Plan for Scalability: Invest in machines that accommodate future production growth or diversification to avoid costly upgrades or replacements.
Indicative Pricing Disclaimer
CNC wood cutting equipment prices vary widely based on machine type, specifications, supplier location, and order size. For example, basic CNC routers suitable for cabinetry might start in the range of $10,000–$30,000 USD, while advanced 5-axis systems can exceed $150,000 USD. Buyers should treat published prices as indicative and conduct thorough due diligence, requesting detailed quotations tailored to their unique requirements and regional considerations.
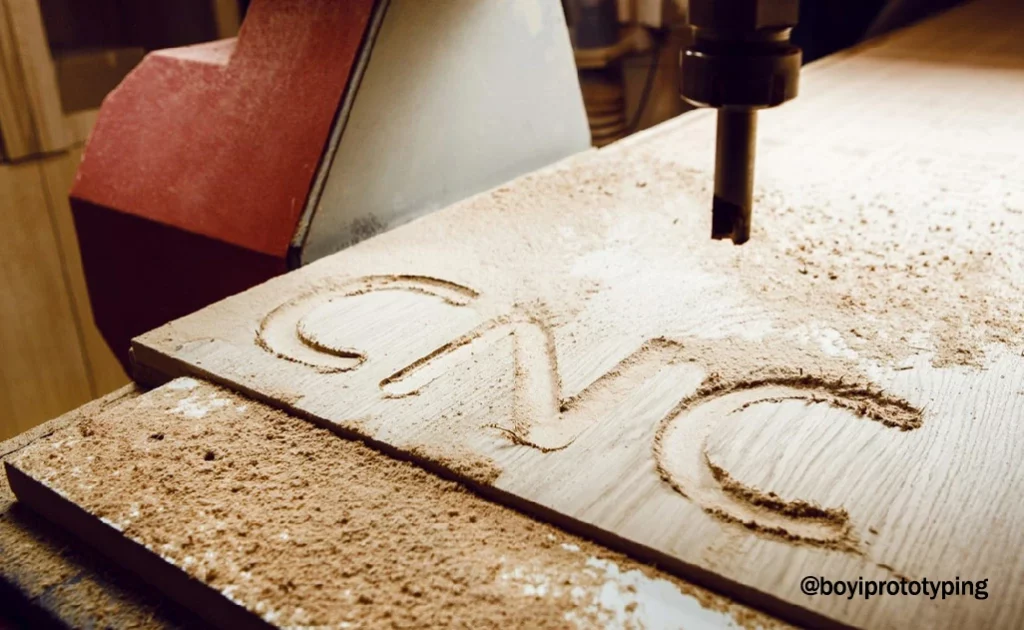
Illustrative Image (Source: Google Search)
By meticulously analyzing these cost and pricing factors, international buyers—particularly from Africa, South America, the Middle East, and Europe—can develop sourcing strategies that balance quality, cost-efficiency, and operational resilience, ultimately driving sustainable growth in their woodworking enterprises.
Spotlight on Potential cnc wood cutting Manufacturers and Suppliers
This section looks at several manufacturers active in the ‘cnc wood cutting’ market. This is a representative sample for illustrative purposes; B2B buyers must conduct extensive due diligence before any transaction. Information is synthesized from public sources and general industry knowledge.
Essential Technical Properties and Trade Terminology for cnc wood cutting
Critical Technical Properties in CNC Wood Cutting
1. Material Compatibility
This refers to the types of wood or wood-based materials (e.g., hardwood, softwood, MDF, plywood) that a CNC machine can effectively process. For B2B buyers, ensuring compatibility with locally sourced or target market materials is vital to avoid costly machine wear or suboptimal cutting quality. Machines designed for hardwoods typically offer higher spindle power and robust build quality.
2. Cutting Tolerance
Cutting tolerance defines the precision level, usually expressed in millimeters or microns, that the CNC machine can consistently achieve. High tolerance machines are essential for products requiring tight fitting parts, such as fine furniture or architectural millwork. Buyers must align tolerance capabilities with product specifications to minimize rework and maintain quality standards.
3. Spindle Power and Speed
Spindle power (measured in kilowatts or horsepower) and speed (RPM) determine the machine’s cutting force and capacity to handle different wood densities and thicknesses. Higher spindle power allows cutting thicker or denser materials faster, which directly impacts throughput and production efficiency. Buyers should match spindle specs with their typical product mix and production volume.
4. Axis Configuration
The number of axes (3-axis, 4-axis, 5-axis) indicates the machine’s ability to move and cut in multiple directions. More axes enable complex 3D shaping and intricate designs without repositioning the workpiece, crucial for bespoke or high-value products. However, increased axes often mean higher costs and require skilled operators.
5. Machine Bed Size
The working area or bed size limits the maximum dimensions of the wood piece that can be processed. For manufacturers handling large panels or furniture components, an adequately sized bed ensures fewer material restrictions and improved workflow. Buyers should consider their product dimensions and future scaling needs when evaluating this property.
6. Software Compatibility and Control Systems
CNC wood cutting machines rely on specialized software for design and operation. Compatibility with widely used CAD/CAM platforms and user-friendly control systems reduces training time and integration issues. Buyers should verify software support and local availability of skilled operators to maximize machine utilization.
Key Industry and Trade Terminology for CNC Wood Cutting
OEM (Original Equipment Manufacturer)
Refers to the company that designs and manufactures the CNC machine. B2B buyers often source directly from OEMs or their authorized distributors to ensure genuine parts, warranty coverage, and technical support.
MOQ (Minimum Order Quantity)
The smallest quantity of machines or parts a supplier is willing to sell in one order. Understanding MOQ helps buyers plan procurement budgets and inventory, particularly important for SMEs or startups in emerging markets.
RFQ (Request for Quotation)
A formal inquiry sent by buyers to suppliers asking for detailed pricing, delivery, and technical specifications. Preparing clear RFQs with precise requirements enables faster, more accurate supplier responses and better negotiation leverage.
Incoterms (International Commercial Terms)
Standardized trade terms defining the responsibilities of buyers and sellers regarding shipping, insurance, and customs. Common terms include FOB (Free On Board), CIF (Cost, Insurance, and Freight), and DDP (Delivered Duty Paid). Clarity on Incoterms prevents costly misunderstandings in international transactions.
Lead Time
The total time from placing an order to receiving the CNC machine. Lead time affects production planning and market responsiveness; buyers should confirm realistic lead times with suppliers, considering regional logistics and customs procedures.
After-Sales Support
Services provided post-purchase, including installation, training, maintenance, and spare parts availability. Robust after-sales support is critical for minimizing downtime and ensuring long-term operational efficiency, especially in regions where technical expertise may be limited.
By understanding these essential technical properties and trade terms, international B2B buyers can make informed procurement decisions, optimize their production capabilities, and establish reliable partnerships within the global CNC wood cutting market.
Navigating Market Dynamics, Sourcing Trends, and Sustainability in the cnc wood cutting Sector
Market Overview & Key Trends
The global CNC wood cutting sector is experiencing robust growth driven by increasing demand for precision, customization, and efficiency across diverse woodworking industries. Key markets—particularly in Africa, South America, the Middle East, and Europe—are witnessing unique dynamics shaped by regional industrialization, export ambitions, and evolving consumer preferences. For example, African manufacturers are rapidly adopting CNC technology to scale furniture and construction component production, capitalizing on expanding urbanization and infrastructure projects. Meanwhile, South American hubs like Brazil leverage CNC systems to boost high-quality furniture exports, integrating advanced machining into traditional craftsmanship.
Technological advancements are a major catalyst shaping sourcing strategies. Multi-axis CNC routers and integrated multi-process centers enable complex designs and faster turnaround, aligning with B2B buyers’ growing needs for product differentiation and shorter lead times. Additionally, the proliferation of smart CNC machines with IoT connectivity enhances predictive maintenance, reducing downtime and operational costs—an attractive value proposition for buyers across all regions.
Sourcing trends reveal a shift towards global supplier diversification to mitigate risks linked to geopolitical tensions and supply chain disruptions. Buyers in the Middle East and Europe increasingly prioritize partnerships with CNC manufacturers offering localized support, training, and spare parts availability to ensure continuity. Cost-efficiency remains critical, but buyers are also scrutinizing total cost of ownership, encompassing energy consumption, software licensing, and logistics complexities. Moreover, digital platforms and virtual demos facilitate remote evaluation of CNC equipment, broadening access for buyers in emerging markets.
In summary, international B2B buyers must navigate a landscape marked by technological innovation, regional production nuances, and supply chain resilience. Strategic sourcing that balances advanced machine capabilities with local service infrastructure and cost transparency is essential to unlocking competitive advantage and sustainable growth.
Sustainability & Ethical Sourcing in B2B
Sustainability is increasingly integral to CNC wood cutting procurement, reflecting global commitments to reducing environmental impact and meeting evolving regulatory and consumer expectations. Woodworking operations traditionally consume significant energy and generate waste, but CNC technology offers pathways to improved resource efficiency through optimized cutting paths, reduced material scrap, and automated quality controls that minimize rework.
Ethical sourcing extends beyond machine performance to encompass the origin and certification of raw materials. B2B buyers prioritizing sustainability seek suppliers who comply with internationally recognized forest management standards such as FSC (Forest Stewardship Council) and PEFC (Programme for the Endorsement of Forest Certification). These certifications assure that wood inputs are harvested responsibly, preserving biodiversity and supporting local communities—an increasingly important factor for buyers in Europe and Australia where environmental regulations are stringent.
Moreover, suppliers offering CNC machines designed for lower power consumption and compatibility with eco-friendly materials (e.g., formaldehyde-free MDF or reclaimed wood) enable buyers to reduce their carbon footprint. Ethical supply chains also demand transparency in labor practices and supplier audits, particularly relevant for buyers sourcing from emerging markets in Africa and South America where labor standards vary widely.
Incorporating sustainability into procurement not only mitigates reputational risks but also unlocks access to green financing and government incentives in many regions. Forward-thinking B2B buyers integrate sustainability criteria into supplier evaluations and contract terms, fostering long-term partnerships that align operational efficiency with environmental stewardship.
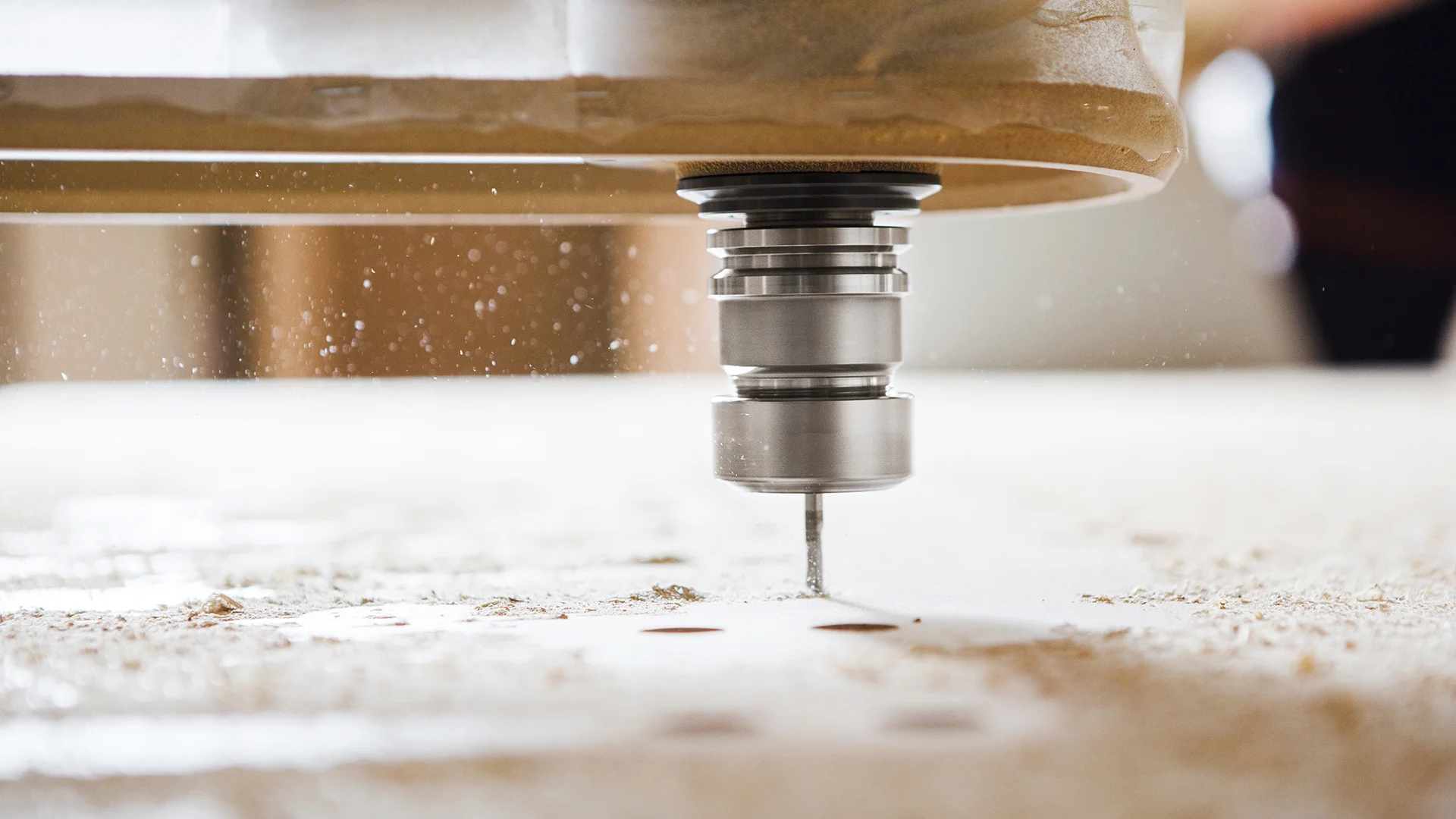
Illustrative Image (Source: Google Search)
Brief Evolution of CNC Wood Cutting Technology
The evolution of CNC wood cutting technology reflects a broader industrial shift towards automation and digital precision. Originating in the late 20th century as adaptations of metalworking CNC machines, early wood CNC routers focused primarily on simple 2D cutting tasks. Over time, innovations in multi-axis control, spindle technology, and software integration have transformed these machines into versatile tools capable of intricate 3D carving, milling, and engraving.
Advances in computer-aided design (CAD) and manufacturing (CAM) software further expanded CNC wood cutting’s capabilities, enabling complex customizations and batch production with high repeatability. The integration of laser and oscillating knife technologies added precision and material versatility, opening new applications in signage and decorative arts.
Today’s CNC wood cutting landscape is defined by smart machines equipped with IoT sensors, adaptive tooling, and AI-driven process optimization. This evolution empowers B2B buyers globally to meet increasingly sophisticated market demands while improving operational agility and sustainability—marking CNC technology as a cornerstone of modern woodworking industries.
Related Video: International Trade Explained
Frequently Asked Questions (FAQs) for B2B Buyers of cnc wood cutting
-
How can I effectively vet CNC wood cutting machine suppliers in international markets?
Start by verifying supplier credentials such as business licenses, certifications (ISO, CE), and years of operation. Request detailed machine specifications, customer references, and case studies relevant to your region or industry. Conduct virtual or onsite audits if possible, and evaluate their after-sales support network, especially local service centers. Check for compatibility with your operational standards and inquire about spare parts availability. For buyers in Africa, South America, the Middle East, and Europe, partnering with suppliers experienced in your regional logistics and regulatory environment reduces risk and ensures smoother procurement. -
What customization options are typically available for CNC wood cutting machines to suit regional wood types and production needs?
Most CNC suppliers offer configurable options such as spindle power, bed size, axis count, tooling systems, and software compatibility. For example, in Africa and South America, machines may require adaptations for local hardwood species or power supply variations. Middle Eastern buyers often need machines optimized for complex architectural designs, while European buyers prioritize precision and compliance with CE standards. Discuss your specific product portfolio, expected production volume, and wood materials upfront to ensure the machine’s features align perfectly with your operational demands. -
What are common minimum order quantities (MOQs) and lead times for CNC wood cutting machines in international B2B transactions?
MOQs vary widely depending on the supplier and machine complexity; some manufacturers allow single-unit purchases, while others require batch orders for custom configurations. Lead times typically range from 4 to 12 weeks, influenced by machine type, customization level, and current production backlog. Buyers from regions with longer shipping durations, such as Africa or South America, should factor in additional buffer time for customs clearance and inland transport. Early engagement with suppliers about production schedules and flexible payment terms (e.g., deposits, letters of credit) can help mitigate delays and cash flow constraints. -
How can B2B buyers ensure the quality and compliance of CNC wood cutting machines before shipment?
Request comprehensive quality assurance documentation, including factory inspection reports, machine calibration certificates, and compliance with international standards like ISO 9001 or CE marking for Europe. Ask for video demonstrations or live virtual tests showcasing machine precision and operational stability. Some suppliers offer third-party inspection services or pre-shipment audits for added confidence. Establish clear acceptance criteria in your purchase contract, specifying performance benchmarks and warranty coverage to protect your investment and avoid costly disputes post-delivery. -
What payment methods are safest for international CNC wood cutting machine purchases?
Letters of credit (LC) and escrow services provide strong security by ensuring funds are released only after contract terms are met. Telegraphic transfers (T/T) are common but carry higher risk unless paired with trusted suppliers and clear payment milestones. For new partnerships, split payments—such as a deposit upfront and balance after delivery or installation—are advisable. Always verify banking details independently and avoid advance full payments. Buyers in emerging markets should negotiate payment terms that accommodate currency fluctuations and local banking regulations to safeguard cash flow. -
How do logistics and shipping impact the total cost and delivery timeline for CNC wood cutting machines?
Freight costs, customs duties, and inland transportation can add 15-30% to machine purchase prices, varying by region. Air freight offers speed but is costly and size-limited; sea freight is economical but slower, often taking 4-8 weeks depending on ports and routes. Buyers in Africa and South America should anticipate longer customs clearance times and potential port congestion. Collaborate with suppliers experienced in international shipping and customs documentation to minimize delays. Consider comprehensive insurance coverage for transit damage and negotiate Incoterms (e.g., FOB, CIF) that align with your logistical capabilities. -
What strategies can buyers employ to resolve disputes with international CNC wood cutting machine suppliers?
Include detailed contractual terms covering product specifications, delivery timelines, warranty obligations, and dispute resolution mechanisms such as arbitration or mediation clauses. Maintain thorough documentation of communications and inspections. In case of disputes, seek dialogue first to negotiate amicable solutions. If unresolved, leverage international trade bodies or chambers of commerce for mediation support. For buyers in regions with less developed legal frameworks, partnering with suppliers who have established international reputations and transparent after-sales policies reduces conflict risks. -
Are there regional differences in after-sales support and maintenance services for CNC wood cutting machines?
Yes, after-sales support quality varies significantly by region. Europe generally offers robust local service centers and spare parts availability, while Africa, South America, and the Middle East may face longer wait times and higher costs for technical assistance. Prioritize suppliers with regional partnerships or authorized service agents to ensure timely machine maintenance and minimize downtime. Training programs for your operators and remote diagnostics capabilities can also enhance operational reliability. Building a local technical support network or collaborating with third-party service providers can further strengthen after-sales resilience.
Important Disclaimer & Terms of Use
⚠️ Important Disclaimer
The information provided in this guide, including content regarding manufacturers, technical specifications, and market analysis, is for informational and educational purposes only. It does not constitute professional procurement advice, financial advice, or legal advice.
While we have made every effort to ensure the accuracy and timeliness of the information, we are not responsible for any errors, omissions, or outdated information. Market conditions, company details, and technical standards are subject to change.
B2B buyers must conduct their own independent and thorough due diligence before making any purchasing decisions. This includes contacting suppliers directly, verifying certifications, requesting samples, and seeking professional consultation. The risk of relying on any information in this guide is borne solely by the reader.
Strategic Sourcing Conclusion and Outlook for cnc wood cutting
Strategic Sourcing: Key Takeaways and Future Directions for CNC Wood Cutting
Navigating the global CNC wood cutting market requires a strategic sourcing approach that balances technology selection, supplier reliability, and regional operational realities. Buyers from Africa, South America, the Middle East, and Europe must prioritize machines that align with their production scale, material types, and market demands—whether that means versatile CNC routers for high-volume furniture manufacturing or advanced 5-axis systems for intricate custom work. Equally important is evaluating supplier ecosystems for after-sales support, warranty coverage, and local service availability, which directly impact uptime and total cost of ownership.
A well-informed sourcing strategy also involves understanding regional nuances, such as power infrastructure in emerging markets or compliance with stringent European standards. This insight empowers buyers to mitigate risks related to logistics, quality control, and maintenance, while unlocking opportunities for growth through innovation and customization.
Looking ahead, the CNC wood cutting landscape will continue evolving with advances in automation, software integration, and sustainable material processing. International B2B buyers should actively engage with trusted global partners, invest in workforce training, and remain adaptable to technological shifts. By doing so, businesses across continents can enhance competitive advantage, drive operational excellence, and seize emerging market opportunities in the dynamic woodworking sector.